
Stone Fruit: Precision Packing
Outcomes and Benefits
Hard Outcomes
- 15% – 20% Worker Productivity increase
- Ease of use – 1 hour training required for managers for a whole season
Soft Outcomes
- Increase fairness by rewarding employees based on fruit count vs on cartons packed
- Prevent unnecessary overtime by keeping workforce motivated and identifying workers that require assistance
- Identify workers requiring retraining due to quality issues being flagged proactively on the scale’s screen
- Uncheatable system with our QR traceability labels
- Live, accurate data every 5s
- More time farming, less time on paperwork
Dashboard and Hardware
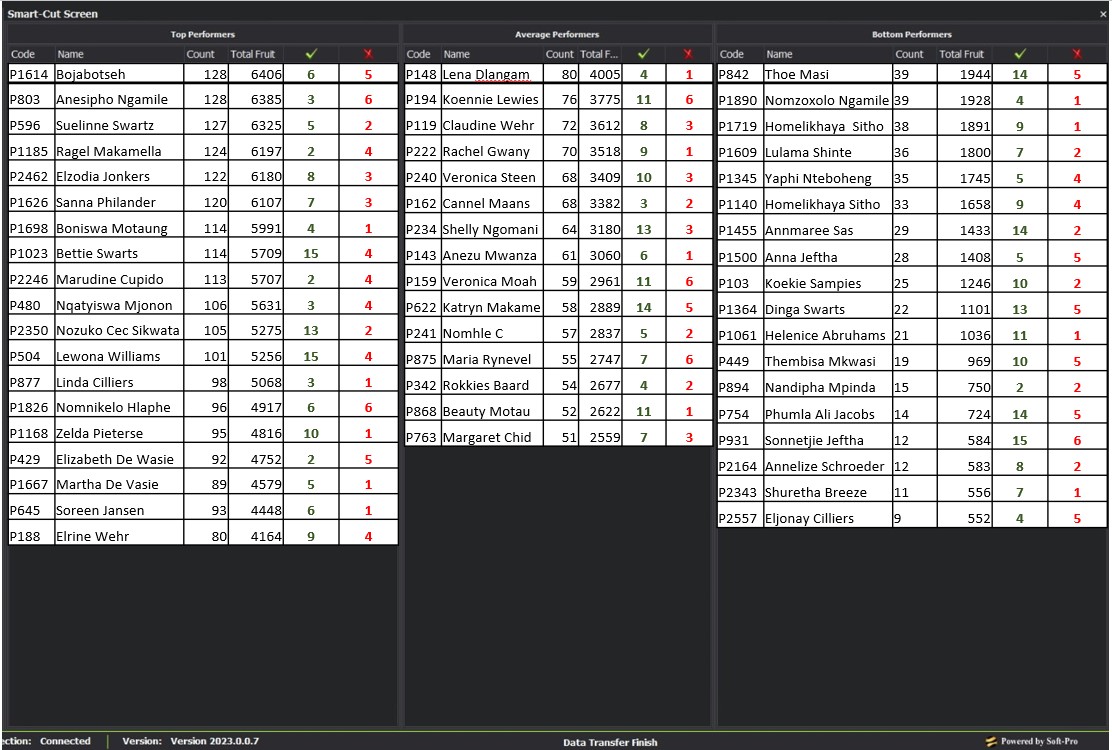
Dashboard showing the employee names sorted by Top Third, Middle Third and bottom third along with their carton count, fruit count, QC Passes and QC Fails.

A Simulation of the sensors and scanners that we use to scan 2 barcodes per box of fruit:
1) Employee name
2) Product details – for fruit count
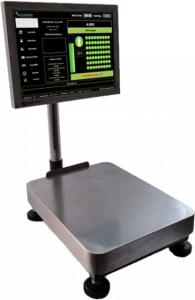
Smart-QC Scale for measuring your product’s weight and flagging any Quality issues
The Setup
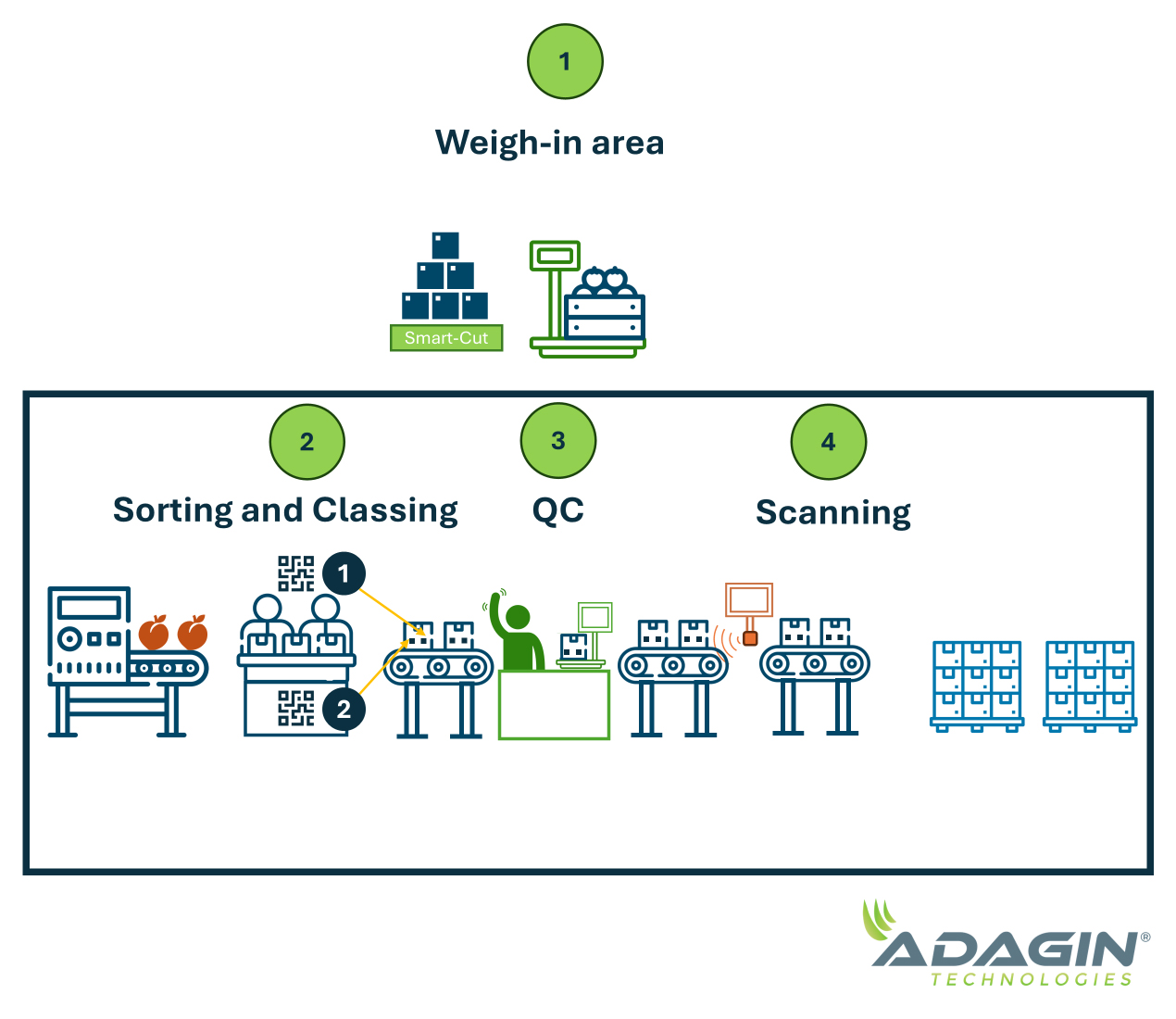
How it Works (Simplified)
1. Weigh-in Area
- Bins coming in from the field are weighed on our Smart-Cut module. Multiple bins can be stacked on top of each other using a forklift and the correct Nett Weight will be logged.
- The scale operator can only start logging bins once the Cultivar and orchard is selected to bring more value to the data being logged.
- The Netto weight is allocated to the orchard from which it comes and it is optional to log the team as well using a Quick Read (QR) labels
- The following data is logged:
- Number of bins
- Average weight per bin
- Nett Weight yield per orchard
- Balance reports
- Number of bins and weight per bin per team
- Number of bins that must still be processed
- Processing speed (bins / hour)
2. Sorting and Classing
- The sorting machine drops the fruit off at the destined / set “Drop” and conveyor belts take the fruit to the workers that fill the cartons / punnets
- To reward the staff fairly, Adagin’s system requires 2 QR labels to be placed on the carton
- The employee’s code and name
- The product details – Cultivar and fruit count
- The system joins the two labels and one can see the number of fruit handlings each person does during the day and not only nr of cartons packed. Fruit count serves as a better productivity measurement
3. Quality Control
- Your quality is your main differentiator in the market. Adagin’s QC module helps you keep your reputation in check. Our QC is able to be set up with your unique criteria along with a point keeping system
- When Quality issues arise, the QC officer is able to log the issue and allocate the correct criteria to it
- Each problem that is logged appears as a red flag on the big screen in the packhouse against the employee’s name. It is now easy to spot any employees that might require retraining.
- The QC station also shows the QC officer on a list which employees have not been checked to be more fair
- When giving workers bonusses, the QC module deducts the workers bonus by the pre-set points allocated to the specific QC mistake
3. Scanning
- Our Smart-Trace system scans each carton and allocates the carton details (Fruit count, cultivar and product type) to the correct worker using the 2 QR labels
- After each scan the screens are update to show the latest ranking with the employees’ QC information next to it.
- Having each carton labelled helps a lot for traceability when problems arise in the market
All of the information above can be seen in real-time on the packhouse server for a holistic view of packhouse speed, employee productivity and quality data on your employees and cultivars.

Frequently Asked Questions
Each employee places a product label next to their personal label that has a lot of information related to the product’s code. It contains Fruit Count, Nett weight, cultivar, carton type and other related information. We only display the fruit count as a productivity measure and the rest of the information is for detailed reports
No, we require the packhouse to have a “Speed up” conveyor belt before the carton’s reach the scanner in order to create a gap between the cartons. This gap is scanned with a beam and once the beam is broken, it indicates to our system that a new carton is going to be scanned. Once the beam is connected again, the system knows the transaction is closed
The system is offline compatible and the system will continue collecting all relevant data. All the data will be sent through to the server once a connection is established again
No, because the system only expects 2 labels per carton, cheating it by placing 2 name labels on the carton for example will just remove the first label’s details and replace it with the second label. The carton will also stand out from the others on the pallet by having too much labels and it will have the employee’s details on it, so everyone will know who tried to cheat the system
Yes, all our dashboards can be exported to excel to be used for internal calculations
Yes, we do the full packhouse service each year for your packhouse. With the service, we also check your network, server, database, update to the latest standard software while calibrating your scales and providing you with a calibration certificate. We do however require calibration specialists to calibrate the 1 ton pallet scale.
Yes, we provide all customers that have an internet connection to their server with remote support by logging in remotely. We also provide remote training
No, the scales operate wirelessly and only has a power cable. The scales can be connected with an ethernet cable, but that is optional and some customers prefer it this way.
Yes, we encourage you to use if for as many as possible products and commodities to extend the usage of the scales, as long as the packing process is similar, it will be able to do it.
Yes, we regularly update our software if it results in a better customer experience