
Table Grapes: Precision Packing
Outcomes and Benefits
Hard Outcomes
- 15% – 20% Worker Productivity increase
- Save money by preventing overpacking of product. In some cases up to 10% revenue increase by preventing overpacking
- Ease of use – 1 hour training required for managers for a whole season
- Save up to 10% of preventable quality issues like underweight products or defects with our QC module
- Less than 1min training required for station users
Soft Outcomes
- Prevent unnecessary overtime by keeping workforce motivated and identifying workers that require assistance
- Identify workers requiring retraining due to quality issues being flagged proactively on the scale’s screen
- Uncheatable system with our QR traceability stickers
- Live, accurate data every 5s
- More time farming, less time on paperwork
Dashboard and Hardware
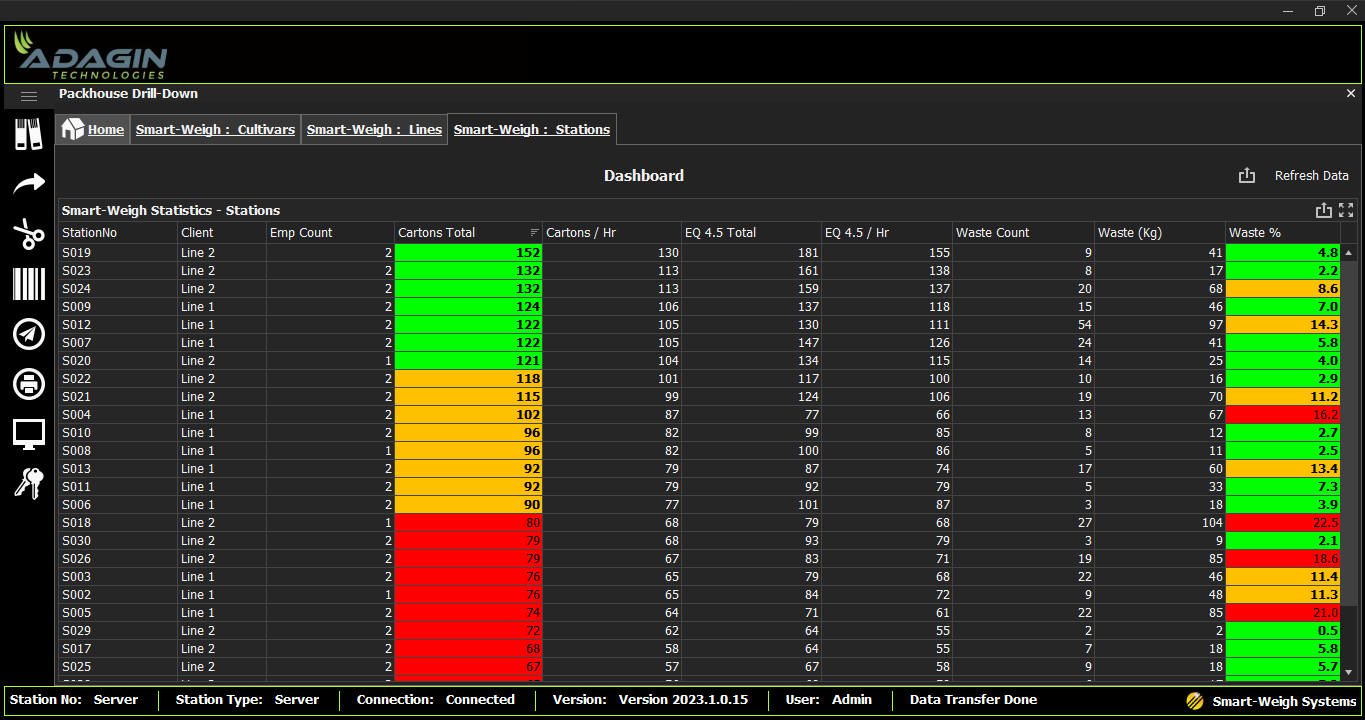
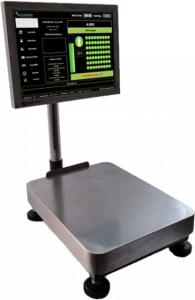
Smart-Scale that can be converted to the module of your choosing
The Setup

How it Works (Simplified)
1. Pre-cooler
- Each feeding line of the packhouse is fitted with a Smart-Cut scale that has an optional scanner.
- The Smart-Cut scale logs the weight of each crate and can scan the crate to allocate the weight to the individual that harvested it
- The scale operator can only start logging crates once the Cultivar and orchard is selected to bring more value to the data being logged.
- The following data is logged:
- Number of crates
- Average weight per crate
- Nett Weight yield per orchard
- Balance reports
- Number of crates and weight per crate per harvester
- Number of crates left in pre-cooler
- Speed per station / line (Crates per hour)
2. Packing
- Each Smart-Weigh station has a team that cleans out the grapes and places it in the correct packaging to be weighed
- The scaler selects the pre-set product on the touch screen and places it on the scale platform
- Each product is weighed and the scale guides the user to get the product to the perfect weight by using arrows and indicators, making it easy to understand
- When the product is on weight, the user confirms it by pressing OK on the screen and the carton is fitted with a traceability sticker allocated to that table
- The following data is logged:
- Output per individual on the station
- Nett-Weight per station
- Waste per station
- Speed per station
- QC logs per station
- Stations ranking in the packhouse
- Cartons weighed vs cartons scanned
- Output per product weighed
3. Scanning
- Each weigh station’s QR sticker is scanned by the Smart-Trace station and only then does the weigh station’s ranking and output increase. This prevents users from cheating the system
- Each QR sticker has a unique ID and therefore it cannot be scanned a second time
- Each palletising line has a Smart-Trace scanner that can scan the whole line’s stations
- Having a unique sticker for each of your boxes helps a lot for traceability. You can log a carton from anywhere on earth down to the time of scan and individuals on the stations using the unique code
- The output per line is displayed in real-time on the Smart-Trace interface
4. Quality Control
- Your quality is your main differentiator in the market. Adagin’s QC module helps you keep your reputation in check. Our QC is able to be set up with your unique criteria along with a point keeping system
- When Quality issues arise, the QC officer is able to press the “Call to QC” button that will block the Smart-Weigh scale from working on without going to the QC officer.
- Each problem that is logged appears as a red flag on the Smart-Weigh scale for line- and packhouse managers to see
- When pressing on the scale’s red flag, the information will be displayed giving feedback on the reason for the QC mistakes
- When giving workers bonusses, the QC module deducts the workers bonus by the pre-set points allocated to the specific QC mistake
All of the information above can be seen in real-time on the packhouse server for a holistic view of packhouse speed, individual station performance and QC output per station, individual and cultivar.
Frequently Asked Questions
The system is offline compatible and no station will stop working. All the data will be sent through to the server once a connection is established again
No, not when you have the Smart-Trace system. The only way to get more cartons for your station is to get more cartons past the Smart-Trace scanner.
Yes, all our dashboards can be exported to excel to be used for internal calculations
Yes, we do the full packhouse service each year for your packhouse. With the service, we also check your network, server, database, update to the latest standard software while calibrating your scales and providing you with a calibration certificate
Yes, we provide all customers that have an internet connection to their server with remote support by logging in remotely. We also provide remote training
Yes, there is a small module built in that allows your employees to verify the weight of each scale. The system also automatically generates a verification report that shows the date and station that was verified to prove that it has been done
It happens instantly, or within 1s.
No, the system does not allow for it. Once the employee logs into a new station, the server will log him or her out of their previous station
No, the scales operate wirelessly and only has a power cable. The scales can be connected with an ethernet cable, but that is optional and some customers prefer it this way.
Yes, we encourage you to use if for as many as possible products and commodities to extend the usage of the scales